Required for a successful binding experience, binding wire is an imperative component. Gracing store shelves in many sizes, colors, and materials – most notably plastic – it is the go-to choice for any craftsman. Steel, aluminum, and even other metallic components are all viable options to consider when choosing binding wire.
Amongst the array of binding wire materials, polypropylene and PVC reign supreme. Polypropylene, with its bounty of vibrant hues, remains the top choice, while PVC offers fewer color options but is far more resilient.
When opting for binding wire, it is essential to take into account the kind of binding that will be implemented. Wire-o binding necessitates a distinct type of binding wire as opposed to comb binding. Moreover, the size of the binding wire must be compatible with the device which will be utilized.
With the supplies and machinery chosen, the only thing left to decide is the size of binding wire for your project. The two standard sizes are 3:1 pitch and 2:1 pitch wire. The former is used for wire-o binding, and the latter is used for comb binding.
After narrowing down the options for binding wire to your preferences, the last factor to consider is its color. Ranging from black and white to clear, there are a variety of different colors available for binding wire, although most of the time it comes in the three aforementioned shades.
When it comes to the vital choices concerning binding type, machine, and wire size and color, the final step is to source binding wire. Several vendors provide the selection required for this project – office supply outlets, the convenience of online purchasing, or specialized binding companies.
It is always a wise decision to opt for quality by obtaining binding wire from a credible retailer. Doing so can guarantee the product’s compatibility with the intended binding machine, as well as its quality standard, thus eliminating any worries of sub-par performance or potential damage caused by inferior materials.
Once the binding wire is acquired, it’s time to fashion the documents together. The particulars of the binding may differ, yet the general approach remains the same regardless of the chosen process.
Upon beginning the binding process, the documents to be bound are first put into the machine. The following step is to feed the binder’s wire through in an orderly fashion. Subsequently, the materials are crimped together in a secure manner to ensure that the contents do not move. When done, the binder is closed and the documents are ready to be handled and used.
Related Product
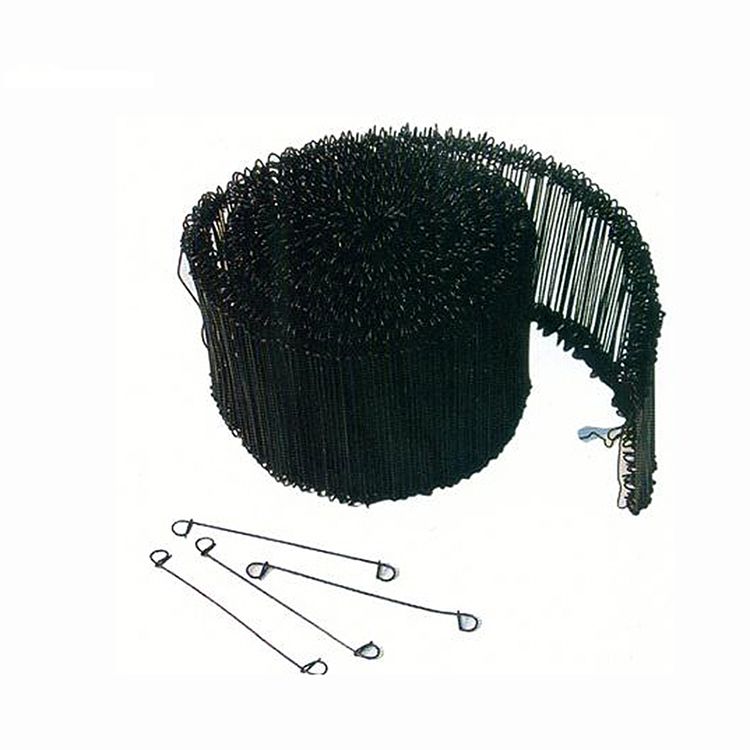
Double Loop Tie Wire
Double loop tie wire material Product Information: Wire diam. 0.5mm—2.0mm Finishes Black Annealed. Galvanized Annealed, Coppered, PVC coated, Stainless steel Wire gauge BWG6 […]
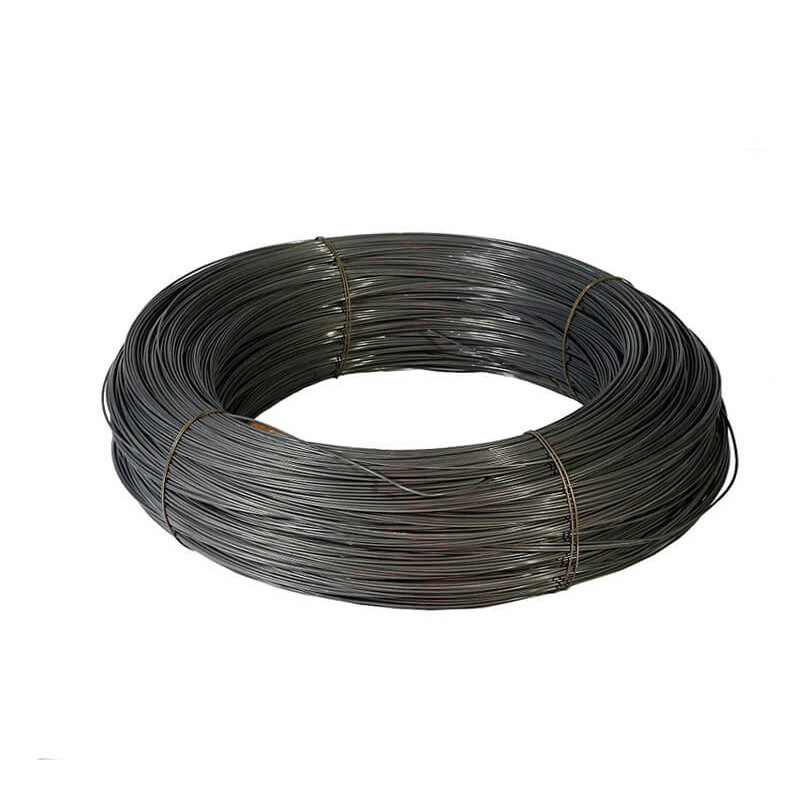
Black Annealed Wire
Product Description: Product name Black Annealed Wire MOQ: No Material Q195,Q235 Delivery time: 20days after payment Surface annealed or as your request Payment terms: T/T,L/C We […]
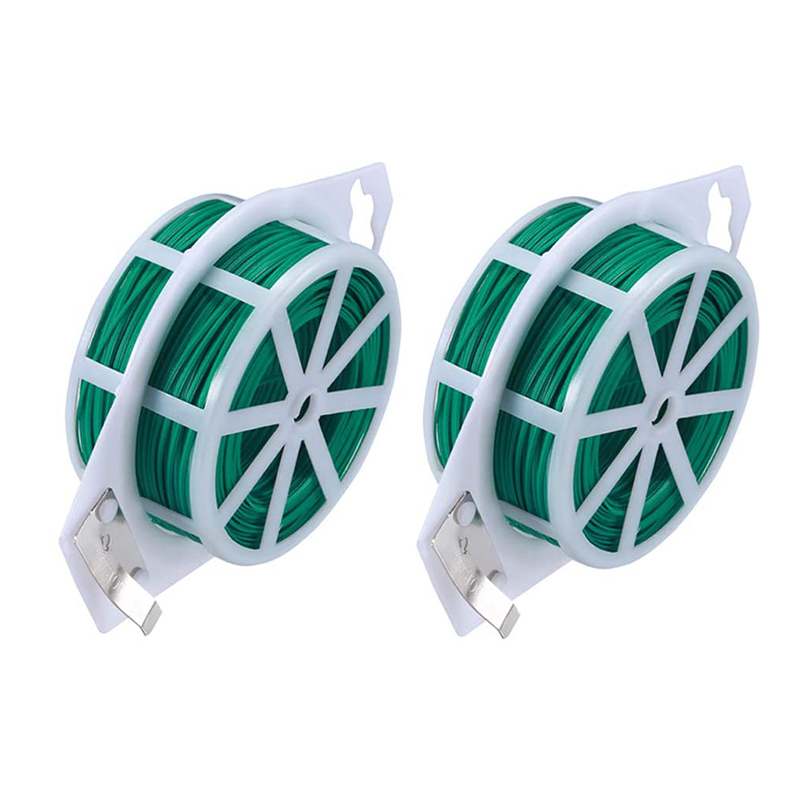
Garden Wire
Product information: The garden shingling is made of pvc plastic and high-quality galvanized iron wire, which is 3 to 4 times faster than any material, and the buckle is loose, the […]
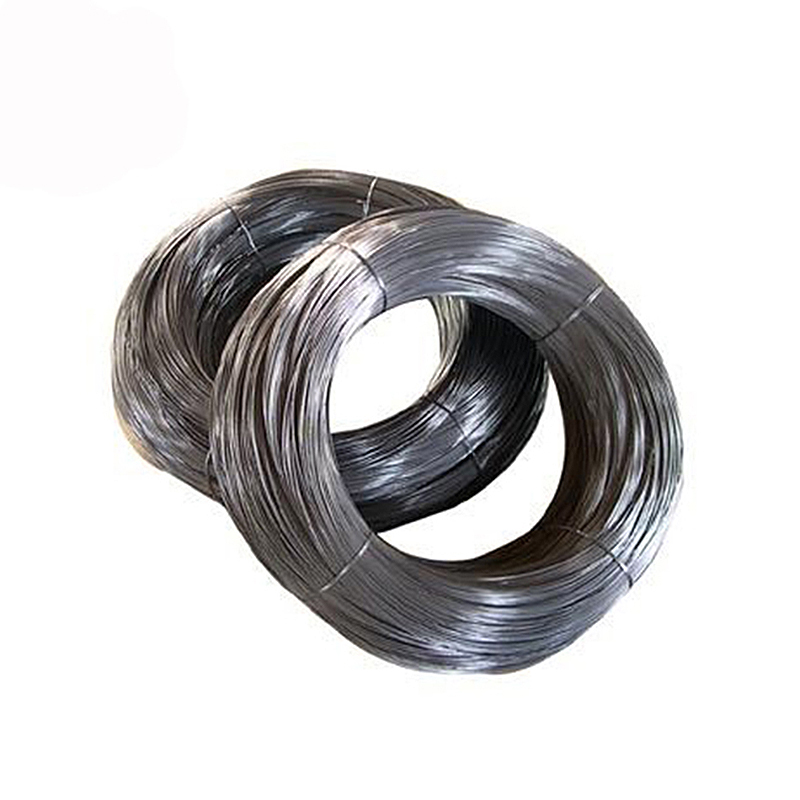
Galvanized Wire
Product information: Product Name Galvanized Wire Package 5kgs/roll, pp film inside and hassian cloth outside or pp woven bag outside 25kgs/roll, pp film inside and hassian […]
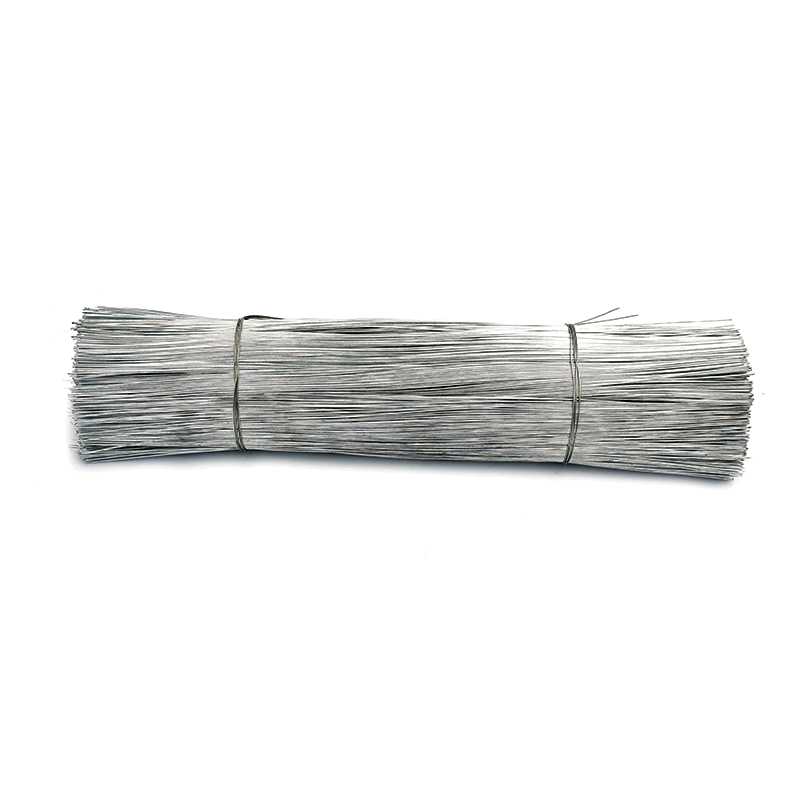
Cutting Wire
Product Description: Product Name Cutting Wire Zinc Coating 30-70g Place of Origin Chinese mainland Tensile Strength 33-50kg/mm2 Material Electro galvanizedHot dipped galvan […]
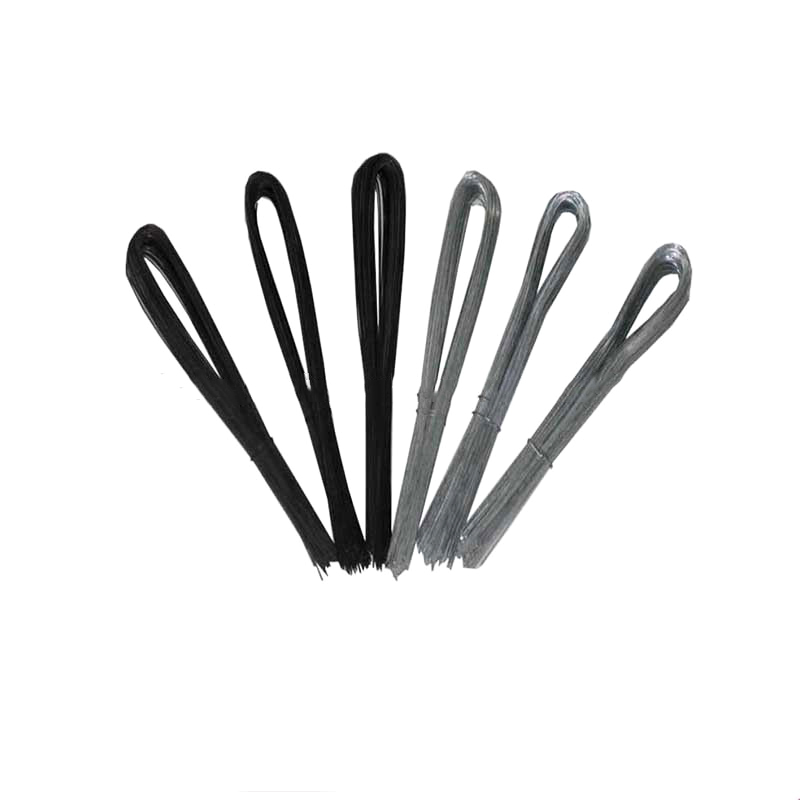
U Type Wire
Product information: Product Name Scaffolding Packing Galvanized Tie Wire Cuttings U Type Binding Wire Material Electro galvanized,hot dipped galvanized,black annealed,PVC coated W […]
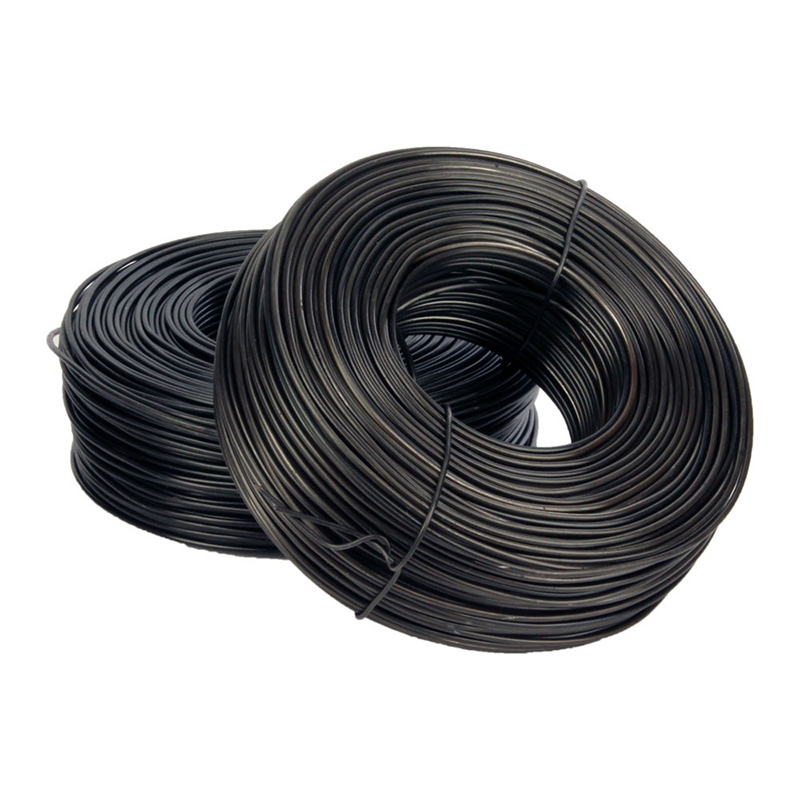
Tie Wire
Production Process of rebar tie wire : Steel rod coil — Wire Drawing — Wire Annealing–Rust Removing–Acid Washing– Boiling– Drying– Zinc Feeding– Wire Coiling. Wires Type 1.Galvaniz […]
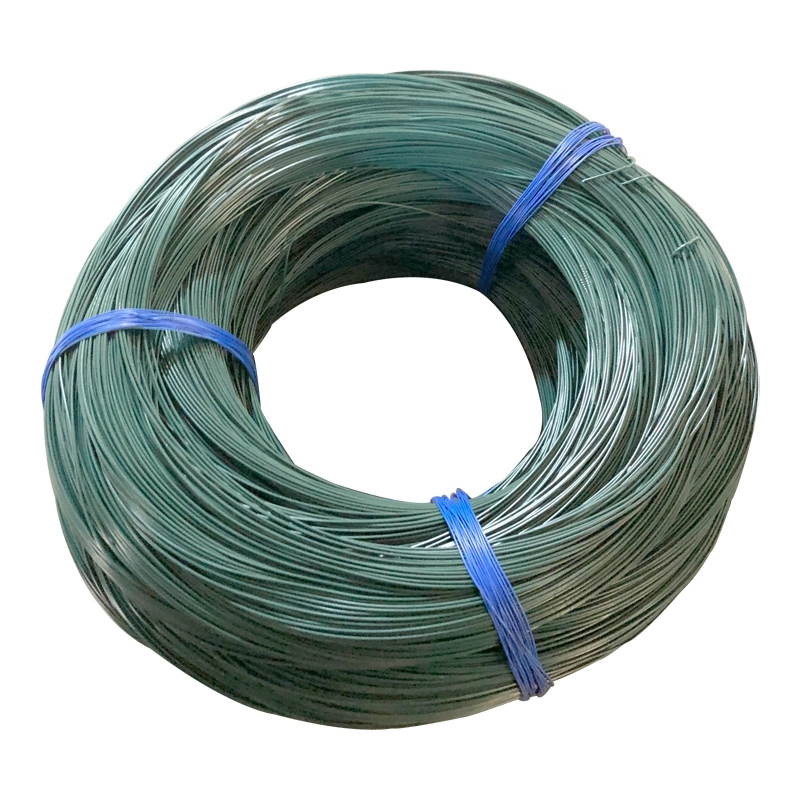
PVC Coated Wire
PVC coated wire, also called plastic coated wire, after high temperature dissolution cooled solid PVC particles uniformly wrapped in high-quality black iron wire and galvanized wi […]
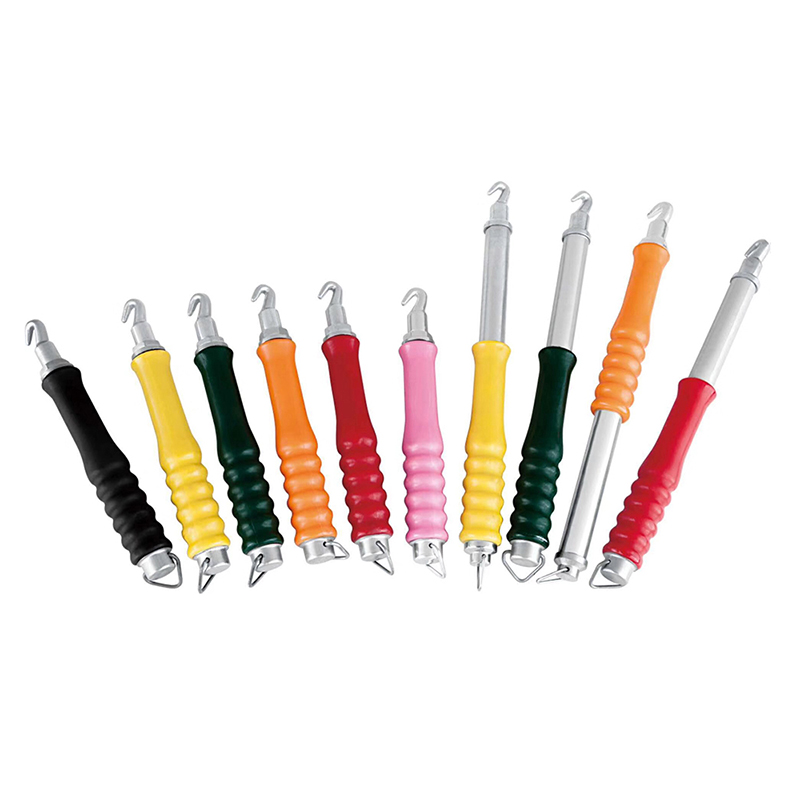
Twister Tool
Handle Twister tool,plastic handle: Weight: 0.4kg Color: Black, blue,yellow ,red etc Material: Carbon Steel Plastic Handle Wire Tie / Tying Hook Tool Twister Wooden Handle […]
Post time: 2023-06-16