ASTM C1063 – ‘Standard Specification for Control Joint Wire Ties’ – issued by the American Society for Testing and Materials (ASTM) outlines the requirements for use of wire ties to firmly attach precast concrete panels. As this is a critical aspect in the building process, compliance with this specification is important.
Precast concrete sections can be securely connected at control joints with the help of a specialized metal tool – the control joint wire tie. It consists of a tie wire that loops around the panel, and a threaded rod inserted through the tie, secured together by a nut in the end.
Precast concrete panels can be fastened together with a control joint wire tie to create a strong shear connection. The tie wire encircles the edge of each panel at the joint, and a threaded rod passes through it. To secure it, the two ends of the rod are tightened together with a nut, creating resistance against wind and seismic forces.
The control joint wire tie attaches precast concrete panels together with an expansion joint, so they can move with the changes in temperature. It works like this: a wire is wrapped around the two panel edges at the control joint, then a threaded rod is shoved through the wire before it’s pulled taut. Finally, the rod ends are attached with a nut to form an accommodating space between the panels.
To ensure a proper drainage path, the control joint requires the installation of tie wire. This is done by maneuvering the wire around the panel at the designated control joint. Afterwards, the tie wire can be fastened with a threaded rod – both ends of which should be locked together with a nut. Doing so will provide an effective outlet for any liquid that may accumulate at the joint.
Depending on the application and environment, control joint wire ties can be crafted with various materials. Steel is often the top choice, while stainless steel is great for more corrosive settings. On the other hand, aluminum provides a lightweight option for areas where weight is a factor.
Depending on the application and the environment, you can find control joint wire ties in several sizes – the most frequent size being 3/8 inch. Other options include 1/2 inch, 5/8 inch, and 3/4 inch.
Depending on the environment and specific needs for an application, there are multiple ways to install a control joint wire tie. Despite welding being the most popular installation method, bolting can be used when weight is an issue, while adhesives come into play if corrosion is the main concern.
Depending on the situation and the conditions, various tools are utilized for the installation of a control joint wire tie. A drill is oftentimes the preferred implement, as it is the most commonly employed instrument. A saw is brought into play when bearing weight is a consideration, while a wrench alleviates corrosion issues.
Depending on the application and ambient conditions, a variety of strategies may be used to install a control joint wire tie. Generally, pre-installation is the go-to technique. However, post-installation will be deployed when there are worries about weight. Alternatively, installation-on-demand is employed in contexts where corrosion may be an issue.
Monitoring the control joint wire tie is a multi-faceted process. Visual assessment remains the most prevalent practice for evaluating these fixtures, but X-rays and ultrasonics come into play in certain circumstances. Corrosion potential may necessitate bringing X-ray technology to the table, while weight considerations indicate that ultrasonic inspection will be more suitable.
To ensure functionality, various testing methods are implemented with regard to the control joint wire tie. These include tension testing – the most typical approach – shear testing for spots where weight is a factor, and fatigue testing for areas that may be subject to corrosion. With each test selection determined by the respective application and environment.
Related Product
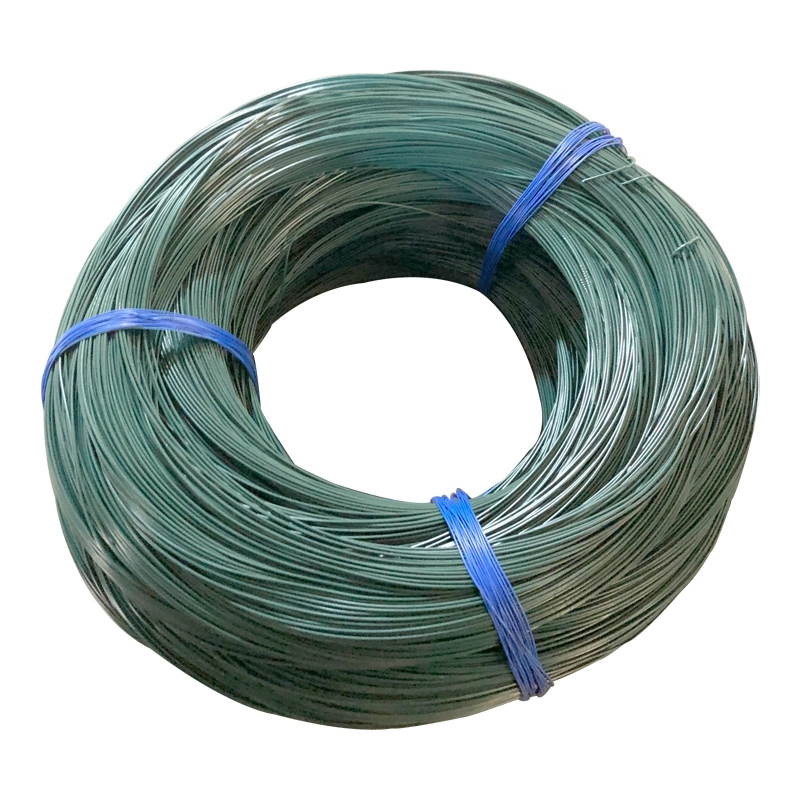
PVC Coated Wire
PVC coated wire, also called plastic coated wire, after high temperature dissolution cooled solid PVC particles uniformly wrapped in high-quality black iron wire and galvanized wi […]
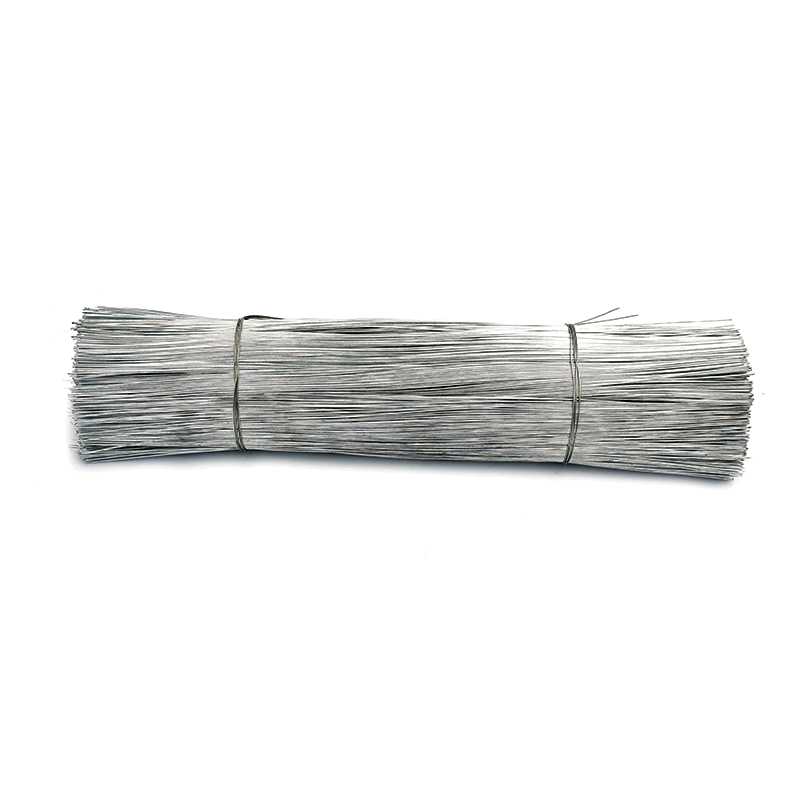
Cutting Wire
Product Description: Product Name Cutting Wire Zinc Coating 30-70g Place of Origin Chinese mainland Tensile Strength 33-50kg/mm2 Material Electro galvanizedHot dipped galvan […]
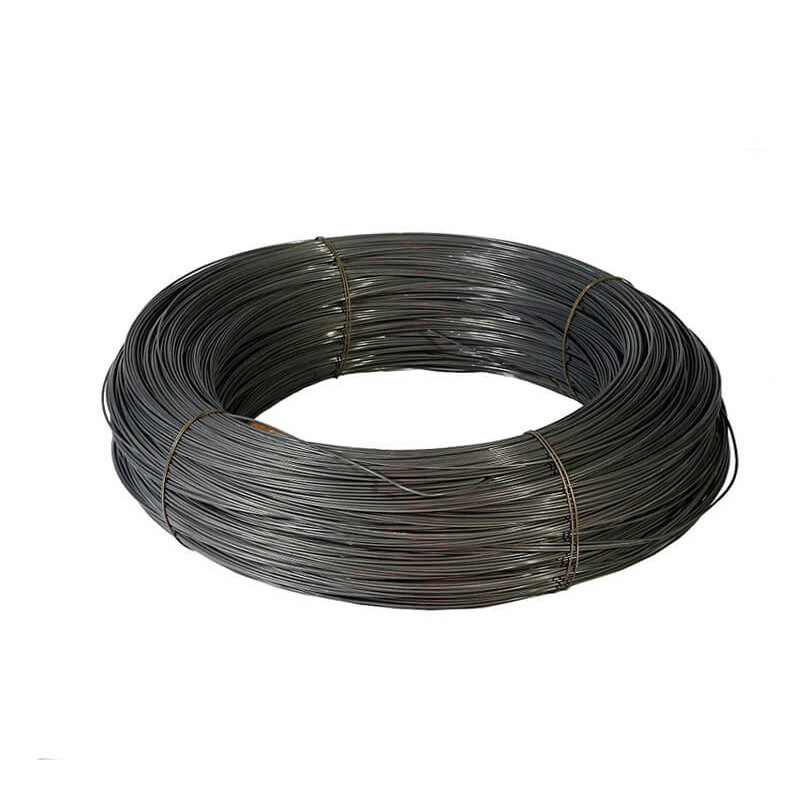
Black Annealed Wire
Product Description: Product name Black Annealed Wire MOQ: No Material Q195,Q235 Delivery time: 20days after payment Surface annealed or as your request Payment terms: T/T,L/C We […]
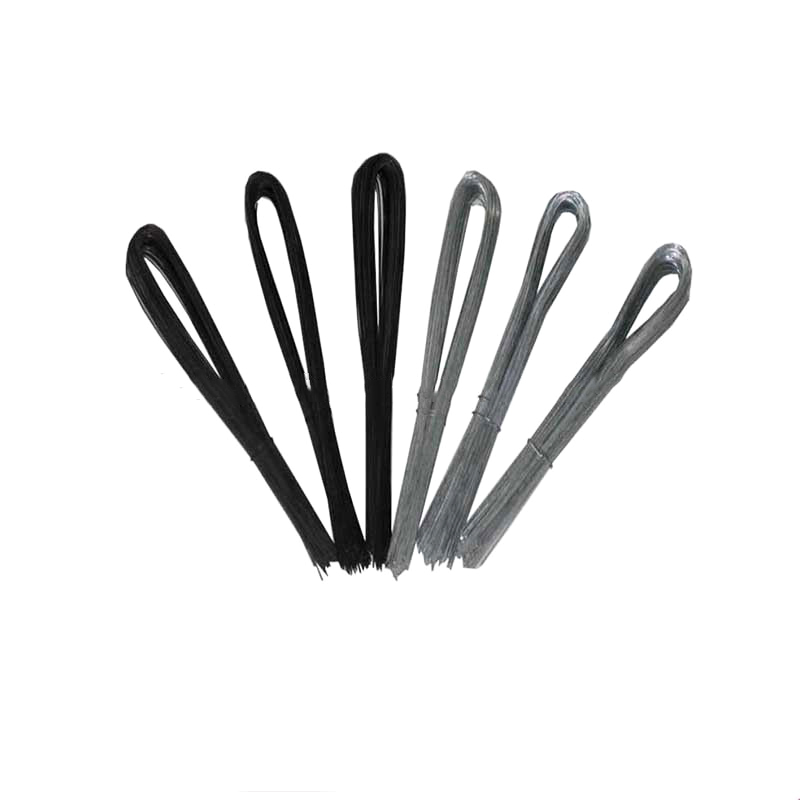
U Type Wire
Product information: Product Name Scaffolding Packing Galvanized Tie Wire Cuttings U Type Binding Wire Material Electro galvanized,hot dipped galvanized,black annealed,PVC coated W […]
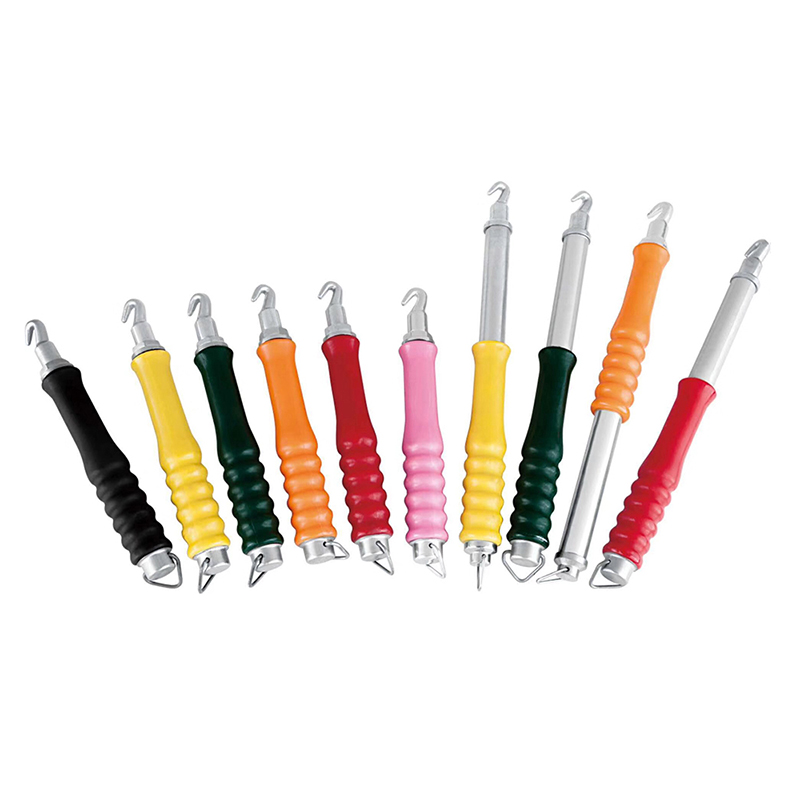
Twister Tool
Handle Twister tool,plastic handle: Weight: 0.4kg Color: Black, blue,yellow ,red etc Material: Carbon Steel Plastic Handle Wire Tie / Tying Hook Tool Twister Wooden Handle […]
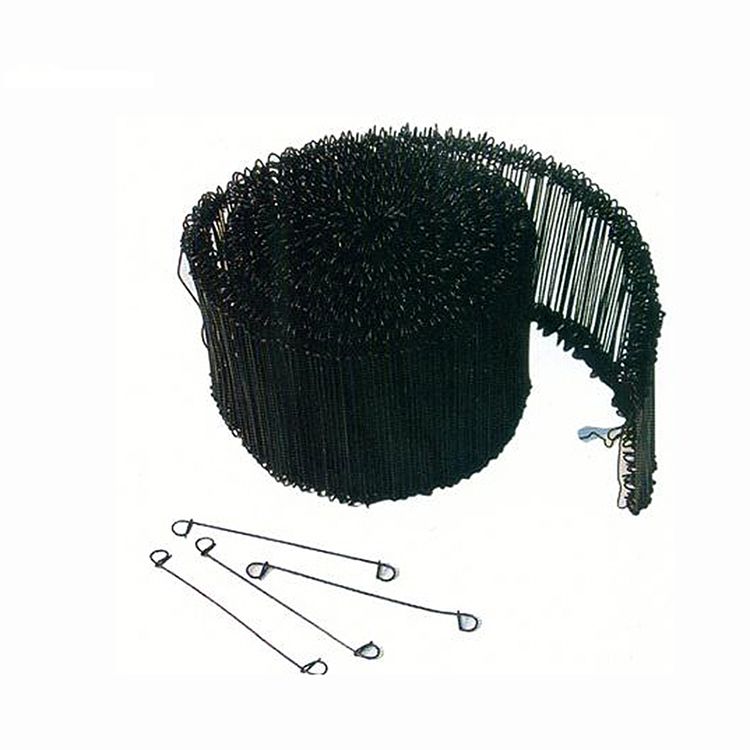
Double Loop Tie Wire
Double loop tie wire material Product Information: Wire diam. 0.5mm—2.0mm Finishes Black Annealed. Galvanized Annealed, Coppered, PVC coated, Stainless steel Wire gauge BWG6 […]
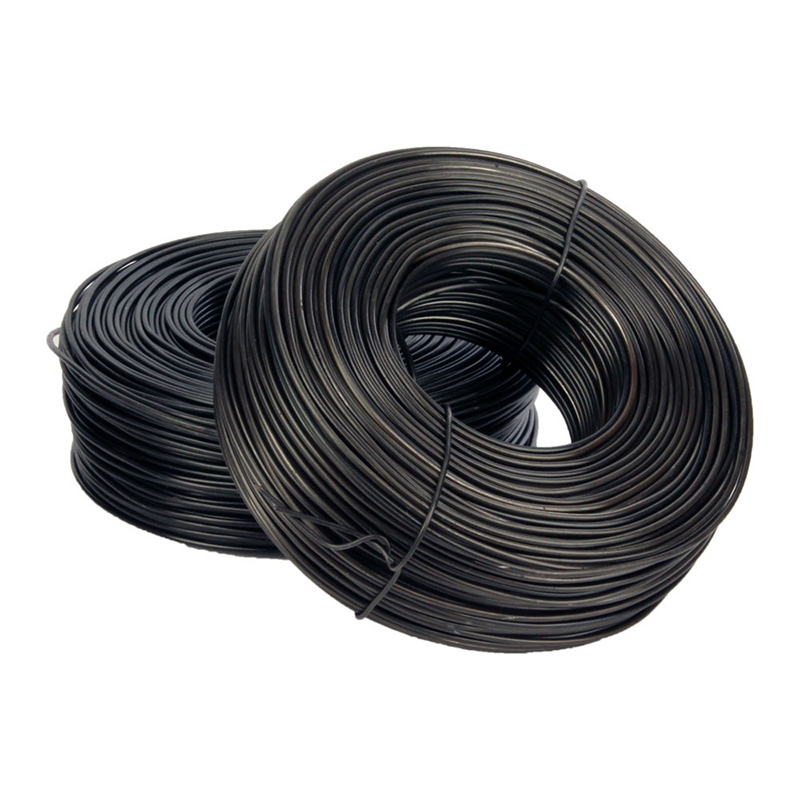
Tie Wire
Production Process of rebar tie wire : Steel rod coil — Wire Drawing — Wire Annealing–Rust Removing–Acid Washing– Boiling– Drying– Zinc Feeding– Wire Coiling. Wires Type 1.Galvaniz […]
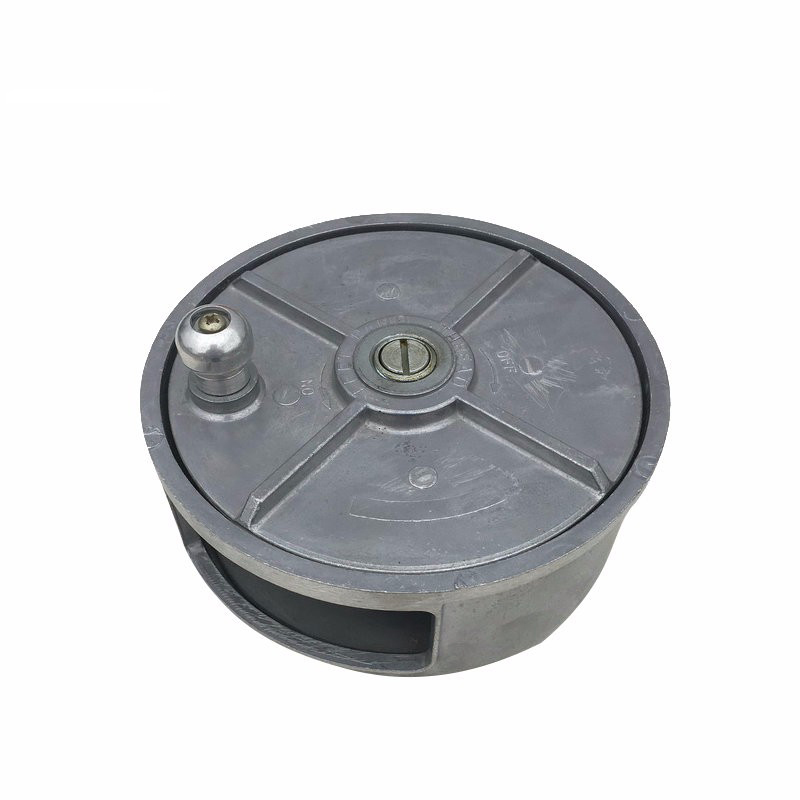
Reel Wire Tool
Product information: Specification of Aluminum Tie Wire Reel Material Plastic & Aluminum Weight 1.95LBS Application Binding Wire MOQ 1000pcs Sample Free Package 5PCS/CARTON &nb […]
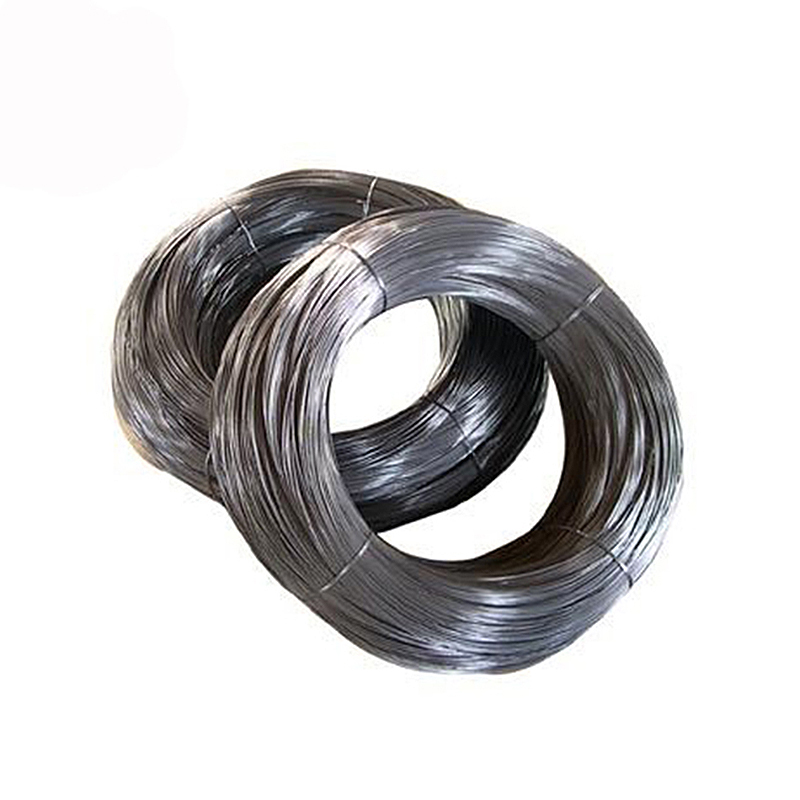
Galvanized Wire
Product information: Product Name Galvanized Wire Package 5kgs/roll, pp film inside and hassian cloth outside or pp woven bag outside 25kgs/roll, pp film inside and hassian […]
Post time: 2023-06-27